Die casting is a metal casting process characterized by forcing molten metal under high pressure into a mold cavity. The mold cavity is created using two hardened tool steel dies, which have been machined into shape and work similarly to an injection mold during the process. Here are the key aspects of die casting:
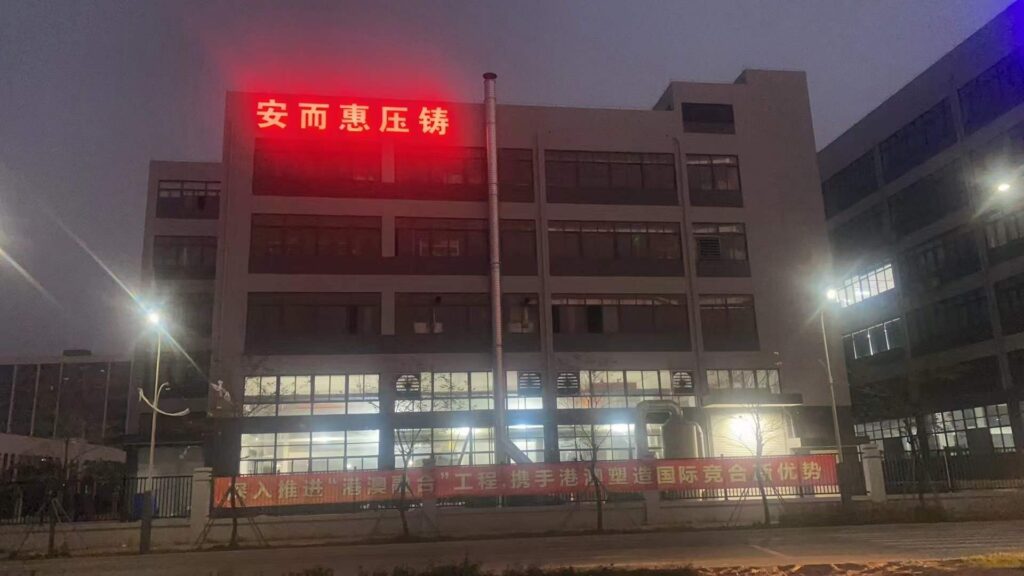
Key Aspects of Die Casting
- Process:
- Injection: Molten metal is injected into the die at high pressure, typically between 10 to 175 megapascals.
- Solidification: The metal cools and solidifies quickly, allowing for high production rates.
- Ejection: Once the metal has solidified, the die is opened, and the casting is ejected.
- Materials:
- Common Metals: Aluminum, zinc, magnesium, copper, lead, and tin are commonly used.
- Alloys: Often, die casting involves using specific alloys to enhance properties such as strength, durability, and corrosion resistance.
- Types of Die Casting:
- Hot-Chamber Die Casting: Suitable for metals with low melting points, such as zinc, lead, and magnesium. The process involves melting the metal in a chamber connected to the die cavity.
- Cold-Chamber Die Casting: Used for metals with higher melting points like aluminum and copper. Here, the molten metal is ladled into a chamber before being injected into the die.
- Advantages:
- Precision and Accuracy: High dimensional accuracy and smooth surface finishes.
- High Production Rates: Capable of producing a large number of castings in a short period.
- Complex Geometries: Ability to cast intricate and complex shapes.
- Applications:
- Automotive Industry: Engine blocks, transmission housings, and other critical components.
- Consumer Electronics: Housings for devices, heat sinks, and connectors.
- Aerospace: Components that require high precision and durability.
Steps in the Die Casting Process
- Preparation of the Mold: The mold is designed and machined from tool steel, comprising two halves: the fixed die half and the movable die half.
- Clamping: The two halves of the die are clamped together in a die casting machine.
- Injection: Molten metal is injected into the die at high speed and pressure.
- Cooling: The metal is allowed to cool and solidify within the die.
- Ejection: The die halves are separated, and the solidified casting is ejected.
- Trimming: Excess material, known as flash, is trimmed from the casting.
Die Casting Equipment
- Die Casting Machine: Available in hot-chamber and cold-chamber types, each suited to different metals and production requirements.
- Dies: Custom-made from tool steel to form the desired shape of the final product.
Considerations
- Cost: High initial cost due to the machining of precise dies and setup but economical for large production volumes.
- Material Limitations: Some metals and alloys are not suitable for die casting due to high melting points or reactivity.
Conclusion
Die casting is a highly efficient and precise manufacturing process that enables the production of complex metal parts at high volumes and with consistent quality. It is particularly well-suited for applications where strength, precision, and intricate designs are required, making it a cornerstone technique in industries such as automotive, aerospace, and consumer electronics.